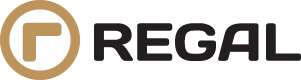
When Waste Management Gisborne secured a long-term contract to carry out kerbside collection for the city, they turned to Regal Haulage for a solution.
Waste Management Gisborne had secured a long-term contract with the Gisborne District Council to provide a kerbside collection service. This included picking up recycling and waste and taking it to the local transfer station. From there, the waste needed to be transported to Tirohia Landfill in the Thames Valley. Operated by HG Leach, the Tirohia Landfill is a Class 1 landfill.
Waste collection operators must adhere to strict discharge regulations to reduce pollution and maintain air quality. This meant, Waste Management Gisborne needed to move the waste on from their transfer station as quickly and efficiently as possible.
To move the rubbish from their transfer station to Tirohia Landfill, Waste Management Gisborne used a tele-handler to load the rubbish into Regal Haulage trucks. However, the tele-handler had a low pay load which resulted in a lengthy load time, and a long wait for Regal’s drivers.
Public safety was also a concern. Peter Muir, Regal’s Sales Manager explains: “With up to six trucks required per day to cope with load outs, there was increasing congestion on site. This led to potential health and safety risks with our large units being on site at the same time as members of the general public were dropping off rubbish.”
"We immediately saw a difference. There was less traffic movement, piles of rubbish were kept to a minimum, and the site was less dangerous for our staff and the public.
"
Regal Haulage proposed to Waste Management Gisborne the purchase of a machine fit for purpose and to take over responsibility of loading the trucks out of hours.
“We replaced a Wheel Loader, where the driver operated the machine close to ground height, with a Material Handler (similar to a digger with grapple attachment), where the cab of the machine could be raised, giving the operator clear view into the unit being loaded,” says Peter. “The operator of the new machine is also able to use the grapple to press the product in the truck down, compacting it in and increasing tonnes carried per load.”
The machine was specifically tailored to the requirements of Waste Management’s site. Kevin Weir, Gisborne Branch Manager of Waste Management NZ Ltd, says Regal’s proposition, and subsequent purchase, resulted in significant benefits for their operations.
“We immediately saw a difference. There was less traffic movement, piles of rubbish were kept to a minimum, and the site was less dangerous for our staff and the public.”
Not only did the new process improve site safety, it resulted in more efficiencies and profitability for both parties.
“We went from having inefficient loading of units (low pay load) to dramatically quicker loading times,” says Peter. “There was greater compaction of product into our units which resulted in increased tonnes carted per load. This increased efficiency justified the use of larger units which could increase cartage capacity per load even further, which in turn meant we were able to give Waste Management a better $/tonne rate.”
Regal now have only two units required most of the time to deal with the load out requirements, as opposed to six and an added benefit has been the greater communication between all staff involved.
Waste Management’s Kevin Weir says the change was incredibly seamless. “Regal employed their own machine operator, who is absolutely brilliant, and they’ve taken over this stage of the process,” he says. “It’s really good for us to know that’s what we’ve got.”